Repairing the construction and operation value chain with good leadership
Any chain is useless with a gap or missing link. But that is exactly what we have in the value chain between building designers/constructors and building users/operators. It matters because this broken chain causes value to be lost to the building occupiers, operators and owners. In almost every building that I observe being handed over, there is a large gap between how the building is designed, constructed and how well it performs for the facilities management teams and building users.
In this article I will look into the UK construction industry problems, the current best-practice models and offer solutions to this deep-rooted problem.
What is the problem?
In theory, buildings are designed to be efficient, low-energy, promote productivity and occupant health. In reality, buildings rarely operate well with common problems manifesting in poor thermal comfort, poor acoustics, poor energy efficiency, troublesome maintenance and complaints by users. It is widely accepted and understood that most ‘low energy’ buildings in fact consume much more energy than they were modelled to do so.
Why is it happening?
The root of the problem, I believe, is how the UK construction industry operates. On one side, we have building designers and contractors who have been commissioned to design and build a building and on the other side we have the building occupiers and operators including FM teams. The two sides only meet briefly at handover. The contractor and designers want to head off to the next project and the occupier just wants to move in. The FM operator is left, literally, holding the baby.
The issues are numerous, I name but a few of the most significant:
- Incorrect design assumptions made about how the building should operate
- Incomplete energy modelling being carried out as Part L of the building regulations does not include user equipment and processes
- Poor build quality
- Underperforming BMS controls systems – that have been poorly specified, programmed and handed over using algorithms that are incorrect
- Commissioning which is only partially carried out and without due diligence. Many systems do not operate as the designer intended and have not been properly checked and signed off
- Poor information being handed from designer/constructor to operator and little time being given to this activity
- Building users and operators misusing the building and its systems
What the industry says
I have questioned a number of construction and operation professionals and the following causes were given:
- “Designers and contractors are simply not appointed correctly – clients do not require involvement beyond practical completion and retention period. There are no penalties nor consequences”
- “There is not enough time at the commissioning and handover stage of the project to do a proper job and short-cuts are taken to achieve practical completion”
- “The RIBA Plan of work 2013 operators and users inclusion is only suggested in its key tasks and they are therefore not followed”
- “Building regulations do not police compliance on energy performance in operation”
- “BMS controls specifications are weak and rely on the controls specialist to get it right”
- “There is little fee allocated to witness testing and commissioning and as such it is left to the contractor to get it right”
- “There is no clerk of works appointed”
- “Design and construction teams too quickly move onto the next project without checking how the building performs”
Best practice models
It would seem that the Australian Construction Industry has this area well under control through their ‘design for performance’ approach where very energy-efficient buildings are routinely achieved using its NABERS scheme.
The UK mirrors this approach through the BSRIA Soft Landings Process or by offering BREEAM post-occupancy evaluations. Guidance is provided by CIBSE in its TM31 Building Log Book Toolkit and Commissioning Management Code M.
What is troubling is that, despite all this guidance and potential support, it is not being taken up by many clients.
Who is responsible?
While it would be good to see legislation and the Building Regulations get tough on post-occupancy performance, I think it is going to be a long time before this happens. We should, as an industry, lobby government for change and, in the meantime, show leadership.
I believe that leadership should consist of better industry awareness around problems, incentives and penalties. It is the ultimate responsibility of clients, but also of architects, surveyors and engineers, to warn clients of the consequences of not taking this area seriously.
Proposed Leadership Model
Leadership in Appointment
- The client should ensure that operational requirements are built into the design consultant’s forms of appointment, ensuring that performance gap is to be managed. This should include incentives and penalties. Ideally a three-year post-occupancy evaluation term should be included with retentions held and released appropriately.
- Engineers should simulate the compliance energy model to Part L and the entire occupied building including people and equipment. This ensures a proper project baseline is set.
- Engineers should be required to properly design the BMS controls system. No more performance specifications.
Leadership in Process
- The operator and occupier should be made part of both the design and handover process and the sign-off, as the RIBA Plan of Work suggests, in key support tasks at Stages 1 to 7. Consider the BSRIA soft landings (or a similar model) to implement the five suggested stages as (1) inception and briefing, (2) design development and review, (3) pre-handover, (4) initial aftercare, (5) one to three years extended aftercare and post-occupancy evaluation
- Employ an independent clerk of the works and commissioning verifier
- During commissioning, make sure that both the consultant and FM team witnesses the commissioning process – adopt CIBSE Commissioning Code M: Commissioning Management
- Documentation. Make sure that the documentation is fit for purpose and that it adopts best practice of CIBSE TM31: Building Logbook Toolkit
- Ensure that the proper time and attention is given to the commissioning stage and user/operator training
- Make sure the FM contractor is correctly appointed and provides maintenance in accordance with CIBSE Guide M: Maintenance engineering and management and SFG20 (the standard for planned maintenance)
- Carry out post-occupancy reviews and audits every quarter in the first year and annually for the following two years (a three year period in total)
- Following this period, adopt a best practice standard such as ISO50001 (Energy Management Standard) to manage energy on an ongoing basis.
This article first appeared in Energy in Buildings & Industry magazine, March 2017.
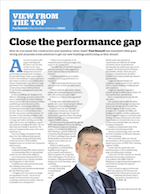